Because E-85 isn’t always 85 percent ethanol, adjust your tune with the help of an ethanol content analyzer. These gauges and sensors are made by the industry’s best brands. Account & Lists Account Returns & Orders.
Free Air calibration is critical to proper oxygen sensor function and accuracy. Here’s a look at how to perform a calibration, how often to calibrate, and what the process accomplishes.
Just like micrometers and dial bore gauges need to be calibrated on a regular basis, wideband O2 sensors must follow a consistent calibration regimen to ensure maximum precision. The fundamental problem with most wideband sensors—whether they’re OE or aftermarket—is that their calibrations are preset for life from the factory. As the typical wideband O2 sensor becomes less accurate over time due to regular wear and tear, it can’t be recalibrated to compensate for wear. Surely, there must be a better way?
To solve this problem, Innovate Motorsports developed a revolutionary new approach to O2 sensor design in the early 2000s. Instead of relying on an O2 sensor’s calibration resistor to calculate air/fuel ratio readings, Innovate’s sensors utilize a patented digital wideband controller that’s built into the sensor cable. This makes it possible to free-air calibrate the O2 sensor at any time in a matter of minutes. During this process, the O2 sensor measures ambient air readings, thus establishing a new baseline to compare against the sensor’s air/fuel measurements. This compensates for the inaccuracy typically caused by sensor wear.
Wear and Accuracy

Although wideband O2 sensors offer a far greater range of latitude than their standard narrowband counterparts, no sensor is immune from wear. Unlike IAT and MAP sensors that take their readings from a clean stream of filtered air, O2 sensors are constantly bombarded by particles of residual fuel, carbon, and soot floating through the exhaust system. Highly modified street and race motors are even less forgiving, often subjecting an O2 sensor to oil past the piston rings and potentially even coolant.
Furthermore, nitrous and forced-induction applications often subject O2 sensors to leaded race fuel and elevated EGTs. The growing popularity of E85 presents challenges as well. “In terms of O2 sensor wear, high EGTs are a concern, as is the high velocity exhaust gas in high horsepower applications,” Felipe Saez of Innovate Motorsports explains. “Ethanol and methanol will not affect sensor life, but these fuels tend to be tuned on the rich side, which does affect sensor life. Condensation can destroy a sensor very quickly as well.”

Maintaining a healthy engine with good ring seal and a proper ECU tune is the best way to minimize these effects, but O2 sensor wear and tear can’t be eliminated entirely. The consequence is a predictable decline in O2 sensor effectiveness. According to Bosch’s published test data, its wideband O2 sensors are accurate to .15 of a point when new, but that figure increases to .29 after 500 hours of use. After 2,000 hours of use, the variation between the measured air/fuel ratio and the actual air/fuel ratio increases to .59 of a point. This means that an indicated air/fuel ratio of 11.76:1 can be as lean as 12.35:1, or as rich as 11.17:1. To most tuners, that is an unacceptably large gap.
Altitude
Granted that Bosch’s lab tests provide an interesting point of reference, they’ re a far cry from the rigors of real-world vehicle operation. When installed on a high-performance application, O2 sensors wear out much more quickly due to elevated EGTs, and richer air/fuel ratios. Detergents and additives commonly found in pump fuel accelerate sensor wear as well.
Even with a fresh, wear-free sensor, the environmental differences between lab testing and real-world driving throw another wildcard into the mix. Bosch calibrates the LSU 4.2 and LSU 4.9 wideband O2 sensors utilized in Innovate’s wideband systems under lab conditions that simulate 14.7 psi of atmospheric pressure at 68 degrees Fahrenheit. That means Bosch’s factory calibrations perform at optimal accuracy only if a vehicle is driven at sea level on a 68-degree day. Anything outside this narrow temperature and elevation window compromises the accuracy of an O2 sensor.
Bosch LSU 4.9 sensors are calibrated in a laboratory setting at sea level and 68 degrees. While they are extremely accurate as delivered, they are still subject to wear and tear, which can dramatically impact tuning and gauge readings.
Easy Calibration
Considering that cars are driven in a wide range of climates and altitudes, free-air calibrating an O2 sensor is paramount in ensuring sensor accuracy. Just like Innovate’s digital wideband sensor controller can compensate for sensor wear, this same technology can be used to compensate for altitude changes by periodically re-calibrating the sensor. Fortunately, free-air calibrating an Innovate wideband O2 sensor is an extremely straight-forward process that only takes a few minutes.
The first step involves disconnecting the O2 sensor cable, then unbolting the sensor from the O2 bung. With the sensor disconnected, the vehicle’s electrical can then be powered up by turning the key to the “On” position. Innovate’s digital gauges will illuminate an error message, while the backlight on Innovate’s analog gauges will display a series of flashes. The system should remain powered up for a minimum of 30 seconds. The next step involves turning the key to the “Off” position, re-attaching the sensor to the cable, and then powering the electrical system with the sensor in free air (not in exhaust system).
Upon turning the key back to the “On” position, digital gauges will display a “HTR” message, while the backlight on analog gauges will steadily blink. This indicates that the sensor is heating up to operating temperature. After 30-60 seconds, digital gauges will display a “CAL” message, while the backlight on analog gauges will stop blinking, indicating that the calibration process is complete. Since the sensor is in free air, it will display the maximum lean value on the gauge.
Finally, after powering the vehicle’s electrical system back down, the sensor can be reconnected to the exhaust system. In a matter of minutes, any Innovate O2 sensor can be calibrated to compensate for wear, as well as for temperature and altitude changes. To ensure maximum precision throughout the sensor’s lifespan, Innovate recommends the following calibration schedule:
When to Calibrate Your O2 Sensor:
Application | Calibration Interval |
Naturally aspirated street car | Calibrate immediately after installing new sensor. Re-calibrate after first 3 months. Thereafter, calibrate once per year or every 20,000 miles. |
Forced induction street car | Calibrate immediately after installing new sensor. Re-calibrate after first 3 months. Thereafter, calibrate twice per year or every 10,000 miles |
Race car running leaded fuel | Calibrate immediately after installing new sensor. Re-calibrate every race weekend. |
Dyno use | Calibrate immediately after installing new sensor. Re-calibrate every 2-3 days. |
While not the most glamorous project-car task, wiring is crucial to a well-running vehicle. Here’re tips, tricks and best practices to make your next install a breeze.
Of all the unwelcome drama a performance vehicle can inflict on its owner, chasing electrical gremlins is perhaps the most frustrating. Just one little wire improperly installed can cripple a car’s performance if the vital engine functions—such as an O2 sensor—are connected to that circuit.
Innovate Motorsports, which manufacturers industry leading wideband controllers, data acquisition equipment, and both digital and analog gauges, says improperly installing its products could result in inaccurate displays, error codes and false information to the vehicle’s ECU or data logger. So, before any electrical problem triggers new adventures in aggravation and futility, the company suggests taking the time to understand the basics of wiring and electrical circuitry.
Do-it-yourselfers often look for the easiest solutions when installing parts. Such a practice is not always due to simple laziness. Some of this approach is driven by questionable advice from friends. Other times it’s relying on outdated methods that don’t apply to modern, sophisticated electrical platforms—even though the task at hand is simply finding a power source or a reliable ground connection.
“Customers tend to tap any 12-volt source on their vehicle without understanding there are multiple circuits on the car dedicated for specific purposes,” says Felipe Saez, customer service technical at Innovate Motorsports.
For example, the Innovate MTX-L Plus is an advanced, stand-alone wideband air-fuel controller and digital readout gauge. It uses a Bosch LSU 4.9 wideband O2 sensor and is compatible with several different fuels. Upon first glance it appears similar to a conventional sensor and gauge combination designed to give the driver specific information. However, the MTX-L Plus is much more sophisticated than a typical oil-pressure or water-temperature gauge. Remember, a wideband sensor requires a heating element that must be kept at the correct temperature to provide an accurate reading.
Within the gauge is a controlling unit that regulates the sensor’s heater. In other words, you can’t just apply 12 volts to the heating element and let it run. If the heating element isn’t at the optimum temperature for the engine rpm or load, then the feedback to the gauge or to an ECU isn’t accurate.
Sound Cards Creative
“The challenge with widebands, as opposed to an oil-pressure gauge, is that we’re heating up that O2 sensor and the power draw is significant,” says Saez. “An oil-pressure gauge may draw a half amp, and that doesn’t fluctuate. You just turn on the gauge and you’re receiving information from the sensor.
“With the MTX-L Plus, we’re heating up the O2 sensor, and the amperage draw changes,” continues Saez. “It changes at wide-open throttle because there is more exhaust flow going over the that sensor. Therefore, the heating has to ramp up. But when you’re cruising around, the draw isn’t that much. But you still need headroom for those changes.”
Now is a good time to refresh memories on the basics of electrical current, which is defined in simplest terms as the flow of electrons through a conductor. Voltage is basically the pressure that pushes the electrical flow. A conventional automotive battery is made up of six 2-volt cells for a total of 12 volts. Some batteries have 2.1-volt cells, for a total of 12.6 volts. Voltage is a potential source of energy for your car, even if the engine is not running and all the accessories are turned off. In other words, if the battery is charged, the voltage is standing by until needed—much like the water pressure is standing by when the outside faucet is closed.
The amount of electron flow is called current, and this activity is measured in amperes, or amps. One ampere is equal to 6.28 billion electrons per second. Using the water flow analogy, think of gallons per minute flowing through a pipe or hose. Now consider a house when a toilet is flushed while someone is taking a shower. Suddenly, there’s a pressure drop with reduced water flow to the shower valve. The cold side of the water flow to the shower head is most affected when the toilet is flushed, and that’s why the shower suddenly becomes scalding hot.
A comparable electrical situation can occur on the vehicle if the wrong circuits are tapped to share current with an Innovate air-fuel gauge. The instructions call for connecting the red wire to a “key on” 12-volt power source that will support a 3-amp current draw.
“One common issue is to tap into the ignition, but your ignition system also draws more power at higher rpm and load,” explains Saez. “So, now you have both the wideband and the ignition system drawing more power. Guess what? The first one that will show symptoms of an issue is the wideband, then you might start seeing ignition misses.”
Other circuits to avoid include the stereo, ECU, lighting or fuel pump. Obviously the power source can’t be directly off the battery or the gauge and sensor will be on all the time and drain it. One option is to tap off an unused power source that doesn’t compromise any other electrical system on the vehicle. For example, the fuse box may have a connection for a power sunroof even though the vehicle doesn’t have that option. The installer would likely need a service manual for the vehicle to trace the proper connection.
A better course of action is to create a stand-alone circuit just for the wideband sensor and gauge using a standard automotive relay.
“Then the power source is directly from the battery but you’re going to trigger the relay to turn off and on with any switched ignition source,” says Saez.
A relay is a basically a device that allows a low amperage circuit to switch a high amperage circuit on or off. As an illustration, a horn has a rather high amperage draw and requires a thick wire to support such a high current flow. But vehicle designers don’t want to run a thick wire from the battery through the firewall to the horn button on the steering wheel, and then return that wire through the firewall again up to the horn mounted on the core support. Instead, they run a small wire from the horn button to a relay that triggers the horn.
Innovate suggests using a 12-volt Bosch/Tyco relay that supports 30 amps. They’re readily available at any auto parts store for just a few dollars.
Every Innovate device also requires a solid ground connection through the black wire on the part’s harness. Again, old-school techniques, such as a dash mounting bolt to the body, may not be effective. “Avoid situations where noise coupling could be an issue,” cautions Saez. “It’s always best to get the ground from a battery negative terminal. Your battery acts like a filter. When in doubt, that’s the best place.”

The next-best location would be the engine block, but avoid bolts that support other ground connections. When contact patches between the different connector lugs stack up, then resistance can build up at that connection. If multiple devices share the same ground connection, the additional resistance can lower the voltage available to each of the devices
Logmein monitors driver download for windows. Running a ground connection from the Innovate device to the negative side of the battery requires at least 18-gauge wire. Saez also suggests using soldered connectors as opposed to crimp style connectors.
“Are there guys who wire up the entire ECU with crimp connectors and don’t have a problem? Sure,” says Saez. “But when a gremlin does surface, that’s exactly the place you want to start looking.”
Even when an installer finds that the ignition circuit can support a wideband sensor and gauge without compromise, noise or electromagnetic disturbances from that wiring can still be an issue that disrupts the wideband’s efficiency.
“The ignition system creates electronic noise or interference through its wires,” says Saez. “All of a sudden you’re getting error codes or the display is going from one extreme to another. Issues with noise are often difficult to troubleshoot because not all symptoms are the same and some ignition systems are noisier than others.
Sound Cards 7.1
In some extreme applications, routing wires too close to an ignition circuit can cause issues. “Remember, it’s a wideband controller. It’s not just a gauge,” sums up Saez. “An oil gauge interprets the signal from the senor but it doesn’t control the sensor. You have to treat the wideband more like an ECU in a sense as it’s controlling the sensor.”
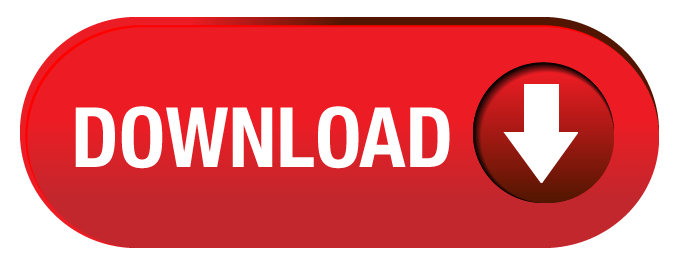